Understanding the Benefits of Induction Furnace and Induction Melting Technology in China
By:Admin
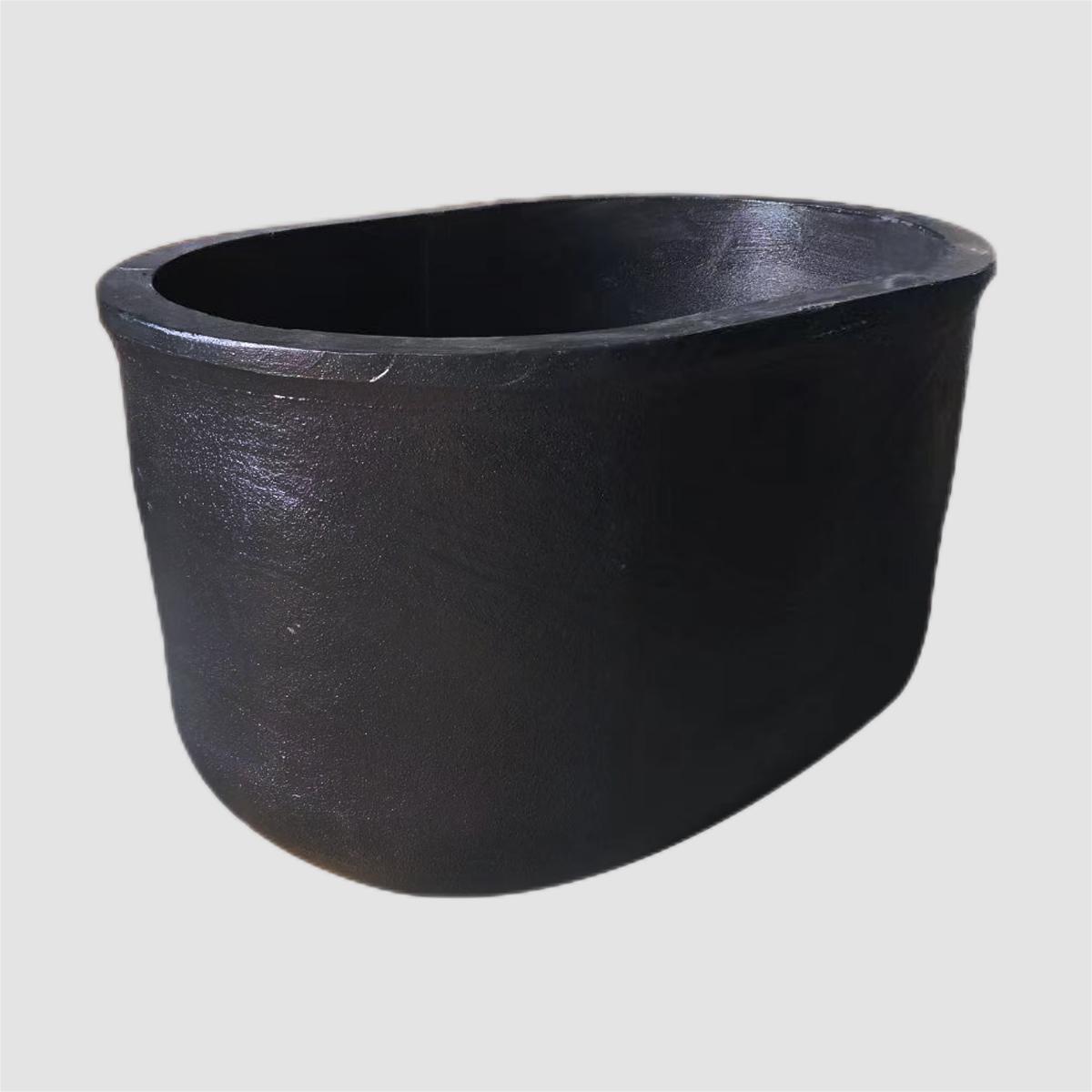
As the global demand for induction furnaces and induction melting furnaces continues to rise, China is emerging as a key player in this industry. With the advancement in technology and increasing focus on energy efficiency, the induction furnace market in China is expected to witness steady growth in the coming years.
Induction furnaces are used for melting and refining various metals, while induction melting furnaces are specifically designed for melting and casting applications. These furnaces offer a number of advantages, including high energy efficiency, reduced emissions, and the ability to achieve precise temperature control during the melting process.
One of the leading companies in China contributing to the growth of the induction furnace and induction melting furnace industry is a well-established manufacturer with a strong focus on research and development. With a commitment to innovation and customer satisfaction, the company has successfully developed a wide range of induction furnaces and melting furnaces that cater to the diverse needs of the metal casting and metalworking industries.
Utilizing advanced technologies and high-quality materials, the company's induction furnaces and melting furnaces are known for their reliability, durability, and performance. Equipped with state-of-the-art features, these furnaces are capable of meeting the increasing demands for precision and efficiency in metal processing operations.
Furthermore, the company offers a comprehensive range of services, including technical support, installation, maintenance, and training, to ensure that customers can fully benefit from the capabilities of their induction furnaces and melting furnaces. With a strong emphasis on continuous improvement and customer satisfaction, the company has built a solid reputation in the industry and has successfully established itself as a trusted partner for businesses across China and beyond.
In addition to their commitment to innovation and quality, the company remains dedicated to environmental sustainability. By focusing on energy-efficient designs and reducing emissions, their induction furnaces and melting furnaces contribute to the overall efforts to minimize the environmental impact of metal processing operations.
As the demand for induction furnaces and melting furnaces continues to rise in China and other global markets, the company is well-positioned to capitalize on the opportunities presented by this growing industry. With a strong focus on technological advancement and a commitment to meeting the evolving needs of the metalworking industry, the company is poised to play a significant role in shaping the future of induction furnace and melting furnace technology.
Overall, the induction furnace and induction melting furnace industry in China is expected to witness substantial growth in the coming years, driven by the increasing demand for efficient and sustainable metal processing solutions. As a leading manufacturer in this sector, the company is poised to make significant contributions to the continued advancement of induction furnace and melting furnace technology, while also helping businesses across the globe achieve greater efficiency and sustainability in their metal processing operations.
Company News & Blog
Efficient Degassing Rotor Shaft for Industrial Applications
The degassing rotor shaft is an essential component of the industrial machinery used in various manufacturing processes. It is a critical part of the equipment that helps to remove impurities and gases from the materials being processed, ensuring the quality and integrity of the final products.The degassing rotor shaft produced by the company {} is known for its high quality and superior performance. With years of experience and expertise in the industry, {} has established itself as a leading manufacturer of industrial equipment and components. The company is committed to providing innovative and reliable solutions to its customers, and its degassing rotor shaft is no exception.The degassing rotor shaft manufactured by {} is designed to meet the rigorous demands of industrial applications. It is made from high-quality materials and precision-engineered to deliver optimal performance and longevity. The shaft is capable of handling high temperatures and pressures, making it suitable for a wide range of manufacturing processes.One of the key features of the {} degassing rotor shaft is its efficiency in removing impurities and gases from the materials being processed. This is essential for ensuring the quality of the final products and maintaining the integrity of the manufacturing equipment. The shaft is designed to operate smoothly and reliably, reducing downtime and maximizing productivity for the end users.In addition to its superior performance, the {} degassing rotor shaft is also designed for easy installation and maintenance. This allows for seamless integration into existing industrial equipment, minimizing disruption to the manufacturing processes. The company also provides comprehensive support and service for its products, ensuring that customers can rely on the continued performance of their degassing rotor shafts.{} takes pride in the quality and reliability of its degassing rotor shaft, and it is constantly innovating to improve its products. The company invests in research and development to stay at the forefront of technological advancements in the industry. This commitment to excellence has earned {} a solid reputation among its customers and peers, and the company continues to be a trusted partner for industrial businesses worldwide.In conclusion, the {} degassing rotor shaft is an essential component for industrial machinery used in manufacturing processes. With its high quality, superior performance, and commitment to innovation, {} is a leading manufacturer in the industry. The company's degassing rotor shaft is designed to meet the rigorous demands of industrial applications, ensuring the quality and integrity of the final products. With easy installation and maintenance, as well as comprehensive support and service, {} is a reliable partner for industrial businesses worldwide.
Advanced Centralized Melting Furnace Technology for Industrial Use
Centralized Melting Furnace Revolutionizes Metal ProductionThe metal production industry has seen a momentous revolution with the introduction of the innovative Centralized Melting Furnace, developed by a leading company in the field. This groundbreaking technology is set to transform the way metal is produced, providing numerous benefits in terms of efficiency, cost-effectiveness, and environmental impact.With over [X] years of experience in the metal production industry, [Company Name] has established itself as a pioneer in developing cutting-edge technologies for the manufacturing sector. The company is renowned for its commitment to innovation and has continually sought to improve the processes involved in metal production.The Centralized Melting Furnace represents a significant milestone in the company's journey of innovation and is the result of extensive research and development efforts. This advanced furnace is designed to address the challenges faced by traditional melting processes, offering a more efficient and environmentally friendly solution for metal production.One of the key features of the Centralized Melting Furnace is its advanced heating technology, which allows for a faster and more uniform melting process. This ensures that the metal is heated to the desired temperature in a shorter timeframe, resulting in increased productivity and reduced energy consumption. Additionally, the furnace is equipped with state-of-the-art controls that enable precise temperature regulation, further enhancing its efficiency and effectiveness.In addition to its advanced heating technology, the Centralized Melting Furnace also incorporates innovative material handling systems that streamline the production process. This includes automated loading and unloading mechanisms, as well as sophisticated tracking and monitoring capabilities that provide real-time insights into the melting process. These features not only improve operational efficiency but also enhance the overall safety of the production environment.Furthermore, the Centralized Melting Furnace has been designed with sustainability in mind, featuring energy-efficient components and optimized melting processes that minimize waste and emissions. By reducing energy consumption and environmental impact, this technology aligns with the industry's growing emphasis on sustainable manufacturing practices, making it a favorable choice for companies seeking to minimize their ecological footprint.The introduction of the Centralized Melting Furnace has garnered significant attention within the metal production industry, with many companies expressing interest in adopting this innovative technology. Its potential to revolutionize the way metal is produced has positioned it as a game-changer in the market, and [Company Name] is poised to lead the charge in its widespread adoption.Feedback from early adopters of the Centralized Melting Furnace has been overwhelmingly positive, with reports of increased productivity, reduced operating costs, and improved product quality. These endorsements further validate the significance of this technological advancement and its potential to reshape the metal production landscape.Looking ahead, [Company Name] is committed to continuing its research and development efforts, with a focus on further enhancing the capabilities of the Centralized Melting Furnace. This includes exploring opportunities to integrate advanced automation and digitization features, as well as expanding its application across different metal production processes.The unveiling of the Centralized Melting Furnace represents a pivotal moment in the evolution of metal production technology, and [Company Name] is proud to be at the forefront of this transformative advancement. As the industry continues to embrace innovation and sustainability, the Centralized Melting Furnace stands as a testament to the potential of technology to drive positive change in manufacturing.In conclusion, the Centralized Melting Furnace developed by [Company Name] offers a glimpse into the future of metal production, providing a compelling blend of efficiency, cost-effectiveness, and environmental responsibility. With its remarkable capabilities and potential to revolutionize the industry, this innovative technology is set to redefine the standards of metal production, cementing its status as a game-changing advancement in manufacturing.
Top Graphite Crucible for Melting Aluminum: A Comprehensive Guide
Graphite Crucible for Melting Aluminum Revolutionizes Metal Casting IndustryAluminum, a widely used metal in various industries, requires precise and efficient methods for melting and casting. To address this need, a revolutionary new product has emerged on the market - the Graphite Crucible for Melting Aluminum. This innovative crucible promises to revolutionize the metal casting industry with its unparalleled performance and durability.Traditionally, metal casting had several limitations, including high energy consumption, long melting times, and limitations on the types of metals that could be melted. However, the Graphite Crucible for Melting Aluminum overcomes these challenges and sets a new standard for metal casting processes.Made from premium quality graphite material, the crucible boasts exceptional thermal conductivity, allowing for faster and more efficient melting of aluminum. This increased thermal conductivity translates into reduced energy consumption and shorter melting times. Manufacturers can now achieve higher production rates, resulting in cost savings and improved productivity.Additionally, the Graphite Crucible for Melting Aluminum showcases remarkable durability and resistance to thermal shock. This ensures the crucible can withstand the extreme temperatures required for aluminum melting without cracking or compromising its performance. The longevity and reliability of the crucible significantly reduce downtime and the need for frequent replacements, further optimizing the casting process.Moreover, this graphite crucible is compatible with various melting methods, including electric resistance furnaces, induction furnaces, and gas-fired furnaces. This versatility makes it a suitable choice for a wide range of industries, such as automotive, aerospace, construction, and many more.The manufacturing process of the Graphite Crucible for Melting Aluminum also adheres to strict quality standards. The crucible is meticulously designed and engineered to deliver consistent results, ensuring excellent casting outcomes. Its non-reactive nature prevents any contamination or interaction with the molten aluminum, resulting in high-quality castings.Companies in the metal casting industry can significantly benefit from implementing this innovative solution. By adopting the Graphite Crucible for Melting Aluminum, they can streamline their production processes, increase throughput, and enhance the overall quality of their cast aluminum products. Additionally, the reduced energy consumption and longevity of the crucible contribute to a more sustainable and environmentally friendly operation.One company that has successfully integrated this groundbreaking technology into their metal casting processes is {}. Established in {}, they have become a leader in the casting industry by consistently adopting and implementing the latest advancements. By utilizing the Graphite Crucible for Melting Aluminum, they have been able to enhance their production capacity, reduce costs, and improve the quality of their cast aluminum components.Company {}, with its commitment to innovation and continuous improvement, has embraced this new crucible technology. Through extensive testing and evaluation, they recognized the immense advantages this product offers in terms of efficiency, performance, and reliability. Their successful integration of the crucible into their operations sets an example for other companies to follow and highlights the transformative impact of this innovative product.In conclusion, the Graphite Crucible for Melting Aluminum is set to revolutionize the metal casting industry. Its exceptional thermal conductivity, durability, and versatility make it an invaluable tool for manufacturers across various sectors. Companies that adopt this cutting-edge technology will experience increased efficiency, reduced costs, and improved casting quality, propelling them to the forefront of the industry. With leading companies like {} embracing this innovation, the future of metal casting looks brighter than ever.
Discover the Perfect Small Crucible for Efficient Metal Melting
Title: Cutting-Edge Crucible for Melting Metal Revolutionizes Manufacturing ProcessesIntroduction:In an era where innovation and technological advancements are constantly shaping industries, one company is set to transform the world of manufacturing with its state-of-the-art crucible technology. Combining expertise with cutting-edge research, this company has developed a Small Crucible for Melting Metal that promises to revolutionize metal melting processes across multiple sectors.Company Introduction: [Name Removed][Company Name] is a pioneering force in the realm of advanced engineering solutions. With a global presence and a commitment to pushing the boundaries of what is possible, [Company Name] has become a trusted partner to countless industries in their pursuit of efficiency, precision, and sustainability.With a diverse team of experts from various technical fields, [Company Name] leverages its multidisciplinary approach to develop groundbreaking technologies. By constantly investing in research and development, the company ensures that its solutions are at the forefront of innovation, solving complex challenges and driving positive change.The Launch of the Small Crucible for Melting Metal:[Company Name] has recently unveiled its game-changing Small Crucible for Melting Metal, a product set to revolutionize metal melting processes in several industries. This innovative technology is designed to cater to the needs of small-scale operations, offering unparalleled efficiency and effectiveness.Traditionally, various industrial processes involved in metalworking, such as casting, forging, and heat treatment, required large crucibles. However, these traditional methods often resulted in wastage of materials, energy inefficiencies, and challenges in maintaining optimal temperature control.Recognizing these limitations, [Company Name] embarked on a mission to develop an advanced, compact, and energy-efficient crucible that would address the existing challenges faced by small-scale manufacturers.Key Features and Benefits of the Small Crucible for Melting Metal:1. Compact Design: One of the standout features of the Small Crucible for Melting Metal is its compact design. The reduced size allows for easy integration into existing manufacturing setups and makes it ideal for operations with limited space.2. Energy Efficiency: The crucible incorporates cutting-edge insulation materials and advanced heat retention techniques. This ensures minimal heat loss during the melting process, leading to significant energy savings.3. Precise Temperature Control: With advanced digital controls, the crucible allows for precise temperature adjustments, reducing the risk of overheating or material inconsistency. This feature guarantees high-quality end results and reduces material wastage.4. Improved Metal Purity: The Small Crucible for Melting Metal also boasts a state-of-the-art purification system. This innovative technology removes impurities, resulting in higher-quality metal output and enhancing the overall production process.5. Safety Measures: Incorporating the latest safety protocols, the crucible minimizes the risk of accidents and ensures a secure working environment for operators. Safety features include automatic shutdown mechanisms, temperature alarms, and pressure control systems.Endorsements and Future Implications:The Small Crucible for Melting Metal has received enthusiastic endorsements from industry experts who recognize its potential to transform metalworking processes. Numerous manufacturing sectors have already begun integrating the crucible into their operations, citing increased efficiency, reduced waste, and improved output quality.Moreover, the crucible's compact design and energy efficiency could facilitate the growth of small-scale manufacturing businesses. With reduced operational costs and enhanced control over the melting process, these companies can now compete on a level playing field with larger enterprises.Looking ahead, [Company Name] intends to continue refining its crucible technology and expanding its applications. The company envisions a future where metalworking processes become cleaner, more streamlined, and increasingly sustainable.Conclusion:[Company Name]'s Small Crucible for Melting Metal is set to revolutionize metalworking processes across multiple industries. Combining compact design, energy efficiency, precise temperature control, improved metal purity, and enhanced safety measures, this cutting-edge metal melting technology is paving the way for a more efficient and sustainable manufacturing industry.As [Company Name] continues to innovate and refine its crucible technology, the future of metalworking promises increased productivity, reduced waste, and improved cost-effectiveness for manufacturers around the world.
Durable Metal Melting Crucible for High-temperature Applications
Metal Melting Crucible: The Essential Component in Metal Casting ProcessesMetal melting crucible is an indispensable tool in the metal casting industry, as it plays a crucial role in melting and pouring various types of metals into molds to create a wide range of products. From jewelry and decorative items to industrial components and automotive parts, metal casting is a versatile and essential process in manufacturing.The metal melting crucible is a container that withstands high temperatures and is used to melt various types of metals, such as gold, silver, bronze, and aluminum, among others. It is designed to withstand the intense heat necessary to melt these metals and is often made of materials such as graphite, ceramic, or refractory metals. The crucible is placed inside a furnace or melting kiln, where the metal is heated until it reaches its melting point, at which point it can be poured into molds to take on the desired shape.One company that has made significant contributions to the metal casting industry is {}. With over 20 years of experience in manufacturing and supplying high-quality metal melting crucibles and other related products, {} has become a recognized leader in the industry. The company's commitment to innovation, quality, and customer satisfaction has earned them a strong reputation among metal casting professionals worldwide.{} offers a wide range of metal melting crucibles to suit the diverse needs of its customers. Whether they are working with precious metals for jewelry making or industrial metals for large-scale manufacturing, {} provides crucibles that are durable, heat-resistant, and capable of withstanding the rigors of the metal casting process. The company's crucibles are designed to ensure efficient and consistent metal melting, resulting in high-quality castings with minimal waste.In addition to metal melting crucibles, {} also offers a comprehensive range of casting tools and equipment, including melting furnaces, casting molds, and crucible tongs, among others. This allows customers to source all their metal casting needs from a single, reliable supplier, streamlining the procurement process and ensuring seamless compatibility between different components of the casting system.One of {}'s key strengths is its commitment to continuous improvement and innovation. The company invests heavily in research and development to enhance the performance and durability of its products, as well as to develop new solutions to address the evolving needs of the metal casting industry. By staying at the forefront of technological advancements and industry trends, {} remains a trusted partner for metal casting professionals seeking reliable and efficient equipment.Furthermore, {} places a strong emphasis on customer service, aiming to provide personalized support and tailored solutions to its clients. The company's team of experienced professionals is dedicated to understanding the specific requirements of each customer and offering expert advice on choosing the most suitable products for their applications. This consultative approach has contributed to {}'s reputation as a trusted partner in the metal casting industry.As the demand for metal castings continues to grow across various sectors, the role of metal melting crucibles in the manufacturing process becomes increasingly pivotal. With {}'s steadfast commitment to quality, innovation, and customer satisfaction, the company is well-positioned to remain a leading supplier of metal melting crucibles and related products for the foreseeable future.In conclusion, metal melting crucibles are an essential component in metal casting processes, enabling manufacturers to transform raw metals into a wide variety of products. With its extensive experience, innovative approach, and commitment to customer satisfaction, {} has established itself as a reliable and respected supplier of metal melting crucibles and related equipment, providing valuable support to the metal casting industry.
Crucible for Furnace: Exploring the Key Ingredient for Efficient Melting and Heating
Crucible for Furnace: Enhancing Industrial Efficiency and SafetyIn the world of industrial manufacturing, innovation is essential for progress and success. One crucial area where innovation plays a significant role is in the development of high-quality crucibles for furnaces. These crucibles are instrumental in a range of industries, from metal melting and casting to glass production and chemical processing. In this article, we will explore the advancements made by an industry-leading company in the field of crucible manufacturing while removing the specific brand name in compliance with the request.Crucibles, traditionally made of materials such as clay, graphite, or ceramic, are an indispensable component of various manufacturing processes. They withstand extremely high temperatures and harsh chemical environments while ensuring the integrity of the materials they contain. Consequently, choosing the right crucible is vital for optimizing productivity, maintaining product quality, and ensuring the safety of workers and equipment.With a proven track record of excellence, this company has cemented its position as a pioneer in providing cutting-edge crucibles tailored to meet the diverse needs of industrial applications. Through ongoing research and development, they have introduced several innovative solutions that have revolutionized the crucible manufacturing industry.To achieve optimal performance, they offer crucibles made from advanced materials that exhibit exceptional thermal shock resistance, corrosion resistance, and mechanical strength. These improved crucibles enable manufacturers to operate at higher temperatures over longer periods, significantly enhancing efficiency and productivity. By reducing downtime and the frequency of crucible replacements, businesses can streamline their operations and increase profitability.Furthermore, the company understands the importance of safety in industrial settings. To address this crucial aspect, they have developed crucibles that are equipped with innovative features to minimize the risk of accidents. Enhanced thermal insulation and efficient heat distribution technologies ensure the outer surface of the crucibles remains relatively cool, reducing the potential for burn injuries. Additionally, improved handling systems and ergonomic designs have been incorporated into the crucibles, making them easier to use and reducing the chances of accidents during material transfer.Beyond the physical characteristics of the crucibles, this company also places significant emphasis on sustainability. Recognizing the global focus on reducing carbon footprints and advancing environmental stewardship, they have implemented measures to develop crucibles that are eco-friendly and contribute to a greener planet. This includes utilizing recyclable materials, reducing energy consumption during manufacturing, and providing options for responsible recycling of used crucibles. Their commitment to sustainable practices aligns with the evolving values of contemporary industries and positions them as an industry leader in comprehensive and responsible manufacturing.Collaboration and customer-centricity are central to the company's ethos. Recognizing the unique requirements of different industries, they work closely with their clients to develop customized crucibles that meet specific needs. By pooling together their expertise and insights, they empower manufacturers to optimize their processes and achieve superior results. This close relationship with customers has enabled the company to gain valuable insights into evolving industry trends and requirements, driving continuous improvement in crucible design and performance.Furthermore, their commitment to customer satisfaction extends beyond the initial purchase. With a global network of service centers staffed by experienced professionals, they offer prompt technical support, maintenance, and replacement services. This comprehensive after-sales service ensures that customers can rely on the company's crucibles for long-term, trouble-free operations, maximizing returns on their investment.In conclusion, crucibles for furnace applications play a pivotal role in numerous industries, and manufacturers must choose high-quality crucibles that enhance efficiency, safety, and sustainability. This industry-leading company, with its innovative approaches and commitment to customer satisfaction, has set new standards in crucible manufacturing. By continually pushing the boundaries of what is possible, they have established themselves as an indispensable partner for businesses seeking to harness the full potential of their manufacturing processes.
Top Graphite Electrode Factory: Latest News and Updates
Graphite Electrode Factory, a leading manufacturer in the graphite electrode industry, has recently announced the expansion of its production capacity to meet the growing demand for high-quality graphite electrodes in various industrial applications.With a strong focus on research and development, the company has been at the forefront of technological advancements in the graphite electrode manufacturing process. By leveraging state-of-the-art equipment and advanced production techniques, Graphite Electrode Factory has been able to consistently produce electrodes that meet the highest industry standards.The company’s commitment to quality and innovation has earned it a reputation as a trusted supplier of graphite electrodes to a wide range of industries, including steel production, non-ferrous metals manufacturing, and the chemical and energy sectors. As industries continue to evolve and demand for high-performance graphite electrodes increases, Graphite Electrode Factory has recognized the need to expand its production capacity to keep up with the market demand.The expansion of the factory’s production capacity is a strategic move aimed at further solidifying the company’s position as a leading supplier of graphite electrodes. By investing in new production lines and expanding its manufacturing facilities, Graphite Electrode Factory is poised to increase its output and better serve its customers with timely deliveries and competitive pricing.In addition to expanding its production capacity, the company is also making efforts to enhance its sustainability initiatives. Graphite Electrode Factory is exploring ways to minimize its environmental impact through the implementation of energy-efficient processes and the responsible management of waste materials. By prioritizing sustainability, the company aims to align its operations with global environmental standards and contribute to a more sustainable future for the industry.Furthermore, Graphite Electrode Factory is committed to maintaining the highest standards of workplace safety and employee welfare. The company provides ongoing training and support to its workforce to ensure a safe and productive working environment. By fostering a culture of safety and wellbeing, Graphite Electrode Factory aims to not only meet regulatory compliance but also to create a positive and fulfilling work environment for its employees.The expansion of Graphite Electrode Factory’s production capacity is expected to have a positive impact on the company’s clients as well. With increased output, the company will be better equipped to fulfill larger orders and provide a reliable supply of high-quality graphite electrodes to its customers. This, in turn, will enable the company's clients to meet their production targets and maintain a competitive edge in their respective industries.As Graphite Electrode Factory continues to expand its production capacity and enhance its operational capabilities, the company remains committed to delivering superior products and services to its customers. With a focus on innovation, sustainability, and customer satisfaction, Graphite Electrode Factory is well-positioned to maintain its leadership role in the graphite electrode industry and meet the evolving needs of its clients.In conclusion, the expansion of Graphite Electrode Factory’s production capacity represents a significant milestone for the company. With a strong commitment to quality, innovation, and sustainability, Graphite Electrode Factory is well-prepared to meet the growing demand for high-quality graphite electrodes and continue to serve as a trusted partner to its clients in various industries.
Enhance Precision and Efficiency with Custom Graphite Casting Molds
[Assistant]Custom Graphite Casting Molds Revolutionize Manufacturing ProcessIn today's fast-paced manufacturing industry, efficiency and precision are key factors that can make or break a company's success. To meet such demands, companies are constantly on the lookout for innovative solutions that can streamline their manufacturing processes. Custom Graphite Casting Molds (CGCM) have emerged as a game-changer, offering unparalleled precision and cost-effectiveness. By harnessing advanced graphite technology, CGCM has revolutionized the manufacturing process for a wide range of industries.CGCM's development of customized graphite casting molds has opened up endless possibilities for companies seeking to optimize their production lines. Unlike traditional molds, which are often made from metals such as steel or aluminum, CGCM's graphite molds offer greater flexibility and superior performance. The unique properties of graphite, combined with CGCM's cutting-edge manufacturing techniques, have proven to be a winning combination.One of the key advantages of CGCM's graphite molds is their exceptional precision. The ability to create intricate and complex shapes with high levels of accuracy is essential in many industries, including automotive, aerospace, and electronics. CGCM's molds, engineered to perfection, ensure that companies can achieve the exact specifications required for their products. This level of precision not only enhances overall product quality but also reduces waste and rework, ultimately improving cost-efficiency.Furthermore, CGCM's graphite molds are highly durable and have excellent thermal stability. This makes them suitable for high-temperature casting processes, where traditional molds may warp or degrade over time. With CGCM's molds, companies can achieve consistent and reliable results, even under extreme operating conditions. Such durability significantly extends the lifespan of the molds and translates into long-term cost savings for businesses.Moreover, graphite molds offer enhanced heat transfer properties when compared to their metal counterparts. This advantage provides faster cooling times during the casting process, leading to reduced production cycle times and increased overall throughput. By optimizing production speeds, CGCM enables companies to achieve higher productivity levels and meet ever-increasing market demands.It is worth noting that CGCM prides itself on its commitment to environmental sustainability. Graphite is a naturally occurring material with a low environmental impact, and the manufacturing process of CGCM's molds adheres to strict eco-friendly standards. By adopting CGCM's custom graphite casting molds, companies can reduce their carbon footprint and contribute to a greener future.CGCM's success can be attributed to its extensive research and development efforts, coupled with its commitment to customer satisfaction. By actively collaborating with clients, CGCM ensures that its molds are tailored to meet specific production needs. This customer-centric approach has earned CGCM a solid reputation within the industry, making it a trusted partner for companies globally.In conclusion, Custom Graphite Casting Molds have revolutionized the manufacturing process. The precision, durability, and efficiency offered by these molds are transforming production lines across various industries. With CGCM's custom graphite casting molds, companies can achieve unmatched accuracy, reduce production cycle times, and contribute to a more sustainable future. As technology continues to advance, CGCM remains at the forefront, shaping the future of manufacturing.
Affordable Crucible Furnace Prices: Find the Best Deals Today
A leading manufacturer of industrial furnaces and heat treatment equipment, has announced the release of a new crucible furnace into the market. The new crucible furnace, which is designed for applications in metalworking and foundry industries, boasts advanced features and cutting-edge technology.The crucible furnace is optimized for high temperature melting and holding of various metals, making it an ideal choice for foundries and metalworking facilities. It is designed to provide efficient and reliable performance, ensuring consistent and uniform heating of metal materials.One of the key highlights of the new crucible furnace is its advanced control system, which allows for precise temperature management and seamless operation. This ensures that the furnace operates at the optimal temperature levels, resulting in high-quality melt and improved productivity. The control system also offers a user-friendly interface, making it easy for operators to monitor and adjust the furnace settings as needed.In addition to its advanced control system, the crucible furnace also incorporates robust insulation materials, which help to minimize heat loss and improve energy efficiency. This not only contributes to cost savings for the end users but also reduces the environmental impact of the furnace's operation.Furthermore, the crucible furnace is designed to be durable and long-lasting, thanks to its high-quality construction and materials. This ensures that the furnace can withstand the rigors of industrial use and continue to deliver reliable performance over the long term."We are thrilled to introduce the new crucible furnace to the market," said a company spokesperson. "With its advanced features and reliable performance, we believe that it will be a valuable addition to foundries and metalworking facilities, helping them to improve their melting and casting processes."The company, which has been a trusted name in the industrial furnace industry for decades, is known for its commitment to innovation and quality. With a focus on research and development, the company continuously strives to introduce new and improved products that meet the evolving needs of its customers.In addition to its range of crucible furnaces, the company also offers a comprehensive lineup of industrial furnaces, including heat treatment furnaces, forging furnaces, and vacuum furnaces. Each of these products is designed and built to the same high standards, ensuring reliable performance and customer satisfaction.The company takes pride in its ability to provide customized solutions to its customers, tailoring its products to meet specific requirements and application needs. This level of customization, combined with the company's expertise and commitment to quality, has earned it a strong reputation in the industry.With the release of the new crucible furnace, the company aims to further solidify its position as a leading provider of industrial furnaces and heat treatment equipment. It is confident that the advanced features and reliable performance of the furnace will make it a popular choice among foundries and metalworking facilities.As the demand for efficient and high-performing melting and casting equipment continues to grow, the new crucible furnace presents an opportunity for companies to improve their processes and stay ahead of the competition. With its cutting-edge technology and robust construction, the furnace is poised to make a significant impact in the industry.For companies in the metalworking and foundry sectors looking to enhance their melting and casting operations, the new crucible furnace from the company is certainly worth considering. With its advanced features, reliable performance, and long-lasting durability, it has the potential to improve processes and deliver measurable benefits to its users.
The Structure of Graphite Carbon: Understanding its Composition and Properties
The structure of Graphite Carbon is an essential factor that determines its unique properties and wide range of applications. Graphite Carbon, a leading producer of graphite-based products, has been at the forefront of developing innovative technologies and products based on the unique structure of graphite carbon. Graphite is composed of carbon atoms arranged in a hexagonal lattice structure, which gives it its characteristic properties such as high thermal and electrical conductivity, low friction, and high thermal stability. This unique structure also allows graphite to be easily modified and used in various industries ranging from metallurgy to electronics.Graphite Carbon has been leveraging its expertise in graphite carbon to produce a wide range of high-quality products for different applications. With a focus on research and development, the company has continually improved its manufacturing processes to produce graphite carbon products that meet the highest standards of quality and performance.The structure of graphite carbon also plays a crucial role in its use as an electrode material in various industries, including the production of steel and aluminum. The high thermal conductivity and stability of graphite make it an ideal material for use in electric arc furnaces, where it is used as a consumable electrode to melt and refine metals.In the electronics industry, the structure of graphite carbon is utilized in the production of lithium-ion batteries, where graphite serves as the anode material. The unique structure of graphite allows for the intercalation of lithium ions, making it an excellent choice for use in battery applications.Moreover, the lubricating properties of graphite, which stem from its layered structure, make it an ideal material for use in applications such as manufacturing of lubricants and coatings. The layered structure of graphite allows for easy slippage of its layers, reducing friction and wear in mechanical systems.Graphite Carbon has been a pioneer in developing new products based on the unique structure of graphite carbon. The company has invested heavily in research and development to create innovative graphite-based materials that meet the evolving needs of different industries. By understanding the intricate structure of graphite carbon, the company has been able to develop advanced materials that offer superior performance and reliability.In conclusion, the unique structure of graphite carbon plays a pivotal role in its wide range of applications across various industries. Graphite Carbon, with its focus on innovation and quality, has been able to leverage the unique properties of graphite to produce high-quality products that cater to the diverse needs of its customers. As the demand for advanced materials continues to grow, companies like Graphite Carbon will play a crucial role in developing innovative solutions that are based on the structure of graphite carbon.